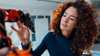
Supercharging industries with AI
Fresh from the stage of Hannover Fair 2024, Rev Lebaredian of NVIDIA and our CEO Roland Busch gave concrete examples of how we’re already making fantasy a reality.
Fresh from the stage of Hannover Fair 2024, Rev Lebaredian of NVIDIA and our CEO Roland Busch gave concrete examples of how we’re already making fantasy a reality.